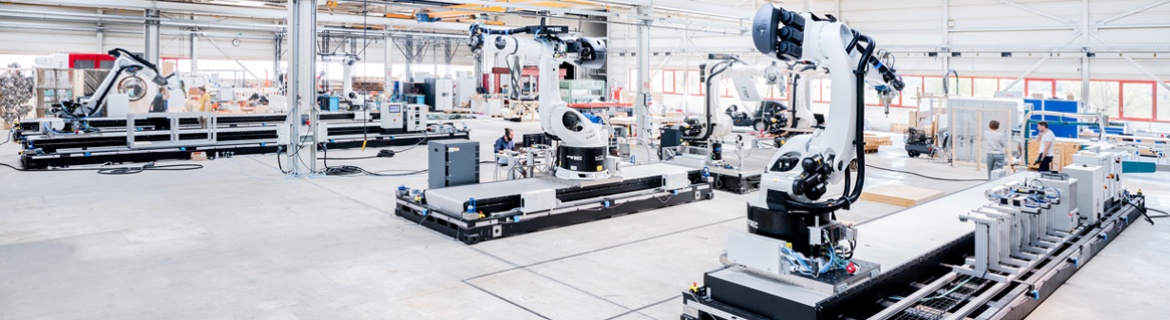
Instrumentation Platform for Off-Site and On-Site Fabrication
The concept of the instrumentation platform for off-site and on-site fabrication has been defined to answer the versatile project-based requests of the AEC industry, which were determined in continuous feedback with the building system developments. Thus, this high level of automation fabrication setup is designed for a maximum of mobility, flexibility and adaptability. Currently based on four ISO-certified containers, the industrial robots on linear axis can be shipped and installed with low effort and using standard equipment. Existing and new hardware can be quickly swapped between the platforms to adapt the machines capabilities to specific fabrication requirements. An open software architecture enables automatic adaptation to the respective system configuration. Additional machinery, such as the autonomous mobile robot, connects this island-based concept for fluid fabrication.
The robotic platform and its components have been developed in the course of the Research Projects “Cyber-Physical Wood Fabrication Platform” (RP 4-1) and “Cyber-Physical Prefabrication Platform for Fibre Composites” (RP 14-1). For the current research two units are dedicated to “Cyber-Physical Fabrication Platform: Fluid Fabrication” (RP 4-2) and two units to “Extention of the Cyber-Physical Prefabrication Platform” (RP 14-2).
The semi-autonomous cyber-physical fabrication system is essential for the prefabrication of flexible, wide-span and multi-storey wood building systems. Two heavy payload industrial robots and customised end effectors equip the system for the manifold additive and subtractive manufacturing steps of softwood and hardwood components in the prefabrication facilities and on site. Augmented reality technology integrates humans, robots and other fabrication actors, such as the autonomous mobile robot in collaborative workflows (Associated Project 29). In this way, this setup breaks free from the usually stringent constraints of high level of automation fabrication concepts.
The additive cyber-physical prefabrication platform for fibre composite building elements is the cornerstone of IntCDC’s fabrication infrastructure for fibrous architecture. It allows for the manufacturing of large-scale fibre parts (Research Project 11-2) and can accommodate a wide range of building system typologies due to its flexible and modular design. Two six-axis industrial robot arms are equipped with bespoke fibre manipulator heads that carry orientation-agnostic impregnation systems to allow for maximum dexterity and reach. Sensor feedback and online path correction make the coreless filament winding process more robust and reliable.